lean six sigma,
six sigma methodologies,
six sigma project management,
5s lean six sigma,
six sigma in operations management,
six sigma in quality management,
six sigma in manufacturing industry,
benefits of lean six sigma,
six sigma principles,
dmaic methodology in six sigma,
six sigma for quality control,
dmaic six sigma,
six sigma process,
lean management six sigma,
six sigma lean manufacturing,
six sigma in strategic management
Six Sigma is a quality management system that helps
companies find and fix problems in their current operations, items, or
services. The intention is to reduce variation throughout production or
business operations by streamlining quality control.
Motorola registered the Six Sigma trademark in 1993. The Greek letter sigma, a
statistical sign for a standard deviation, is referenced in the name. Because a
Six Sigma process is supposed to be defect-free 99.99966% of the time, with 3.4
defective features for every million opportunities, Motorola chose to use the
term. Although Motorola originally intended for its own production operations
to achieve this goal, it soon gained popularity and became a standard.
Is Your Organization Experiencing These Problems?
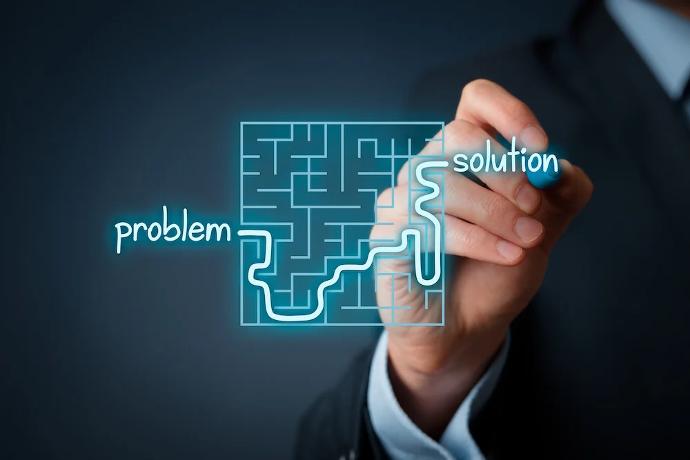
Indeed, an increasing number of organizations face persistent challenges stemming from the dynamic environment. Key issues include:
Ineffective inventory control.
Excessive resource wastage.
Low employee involvement.
Customer dissatisfaction.
Decreasing profitability.
The Comprehensive Impact of Lean Six Sigma on Businesses
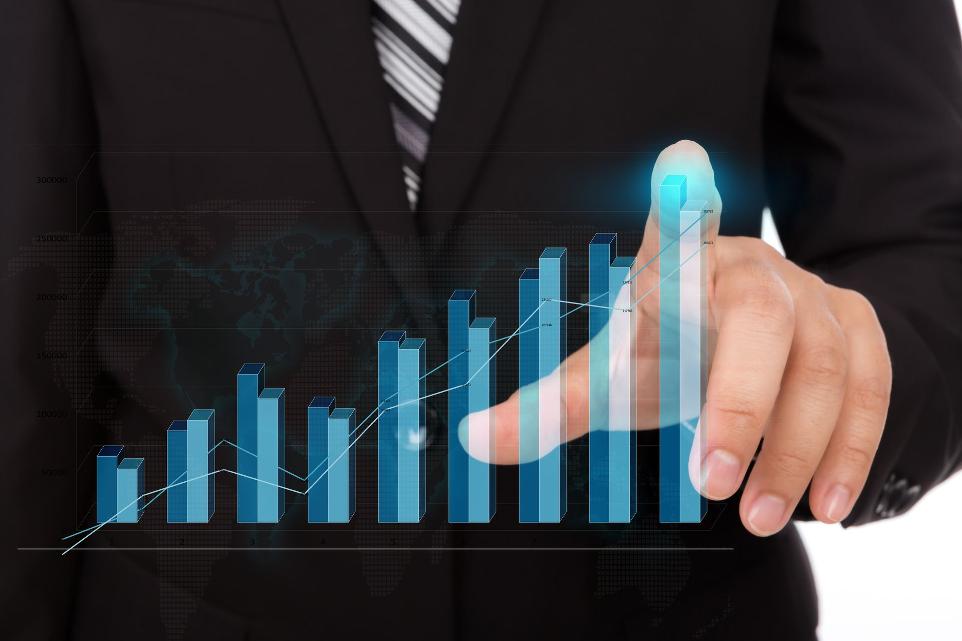
Six Sigma Benefits for Businesses
Any size company can use Lean Six Sigma (LSS).
Medium-sized and small companies can achieve the same level of success as giant
businesses. Smaller companies might be quicker because they have fewer
employees and less complexity to deal with.
For companies seeking a road map to efficiently accomplish their strategic
objectives, this approach is effective. By using it, a company can save
expenses and boost income while freeing up resources to offer value where it
most needs them.
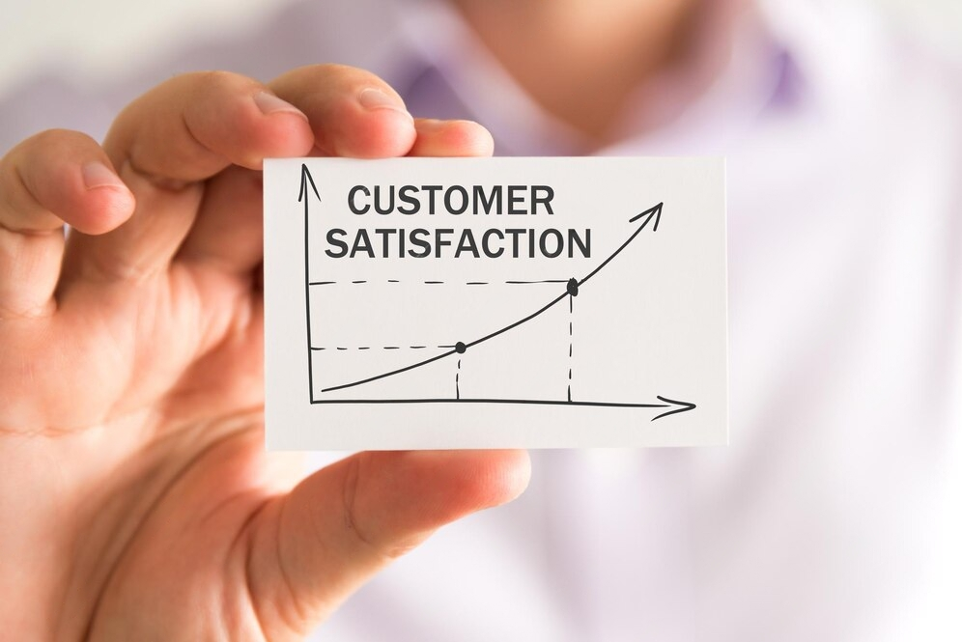
Six Sigma Benefits for Customers
Customers that consistently receive excellent
products and services are the real winners.
Six Sigma supports the greatest standards of quality and dependability for its
services and products, which promotes customer happiness. With careful defect
removal and reduced unpredictability, this process enables organizations to
exceed customer expectations.
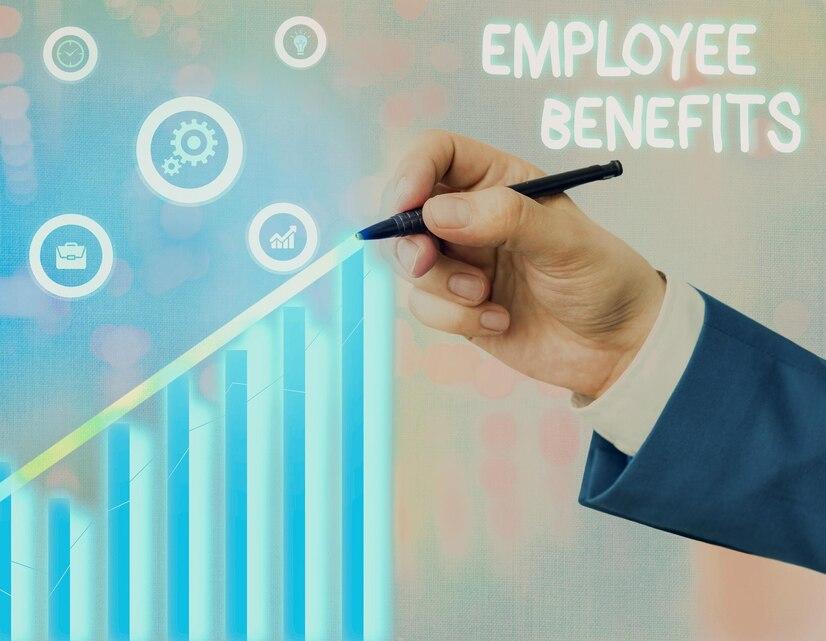
Six Sigma Benefits for Employees
Engaging employees in the process of improving
their own processes is one way that Six Sigma not only increases profit margins
but also has a beneficial impact on staff satisfaction.
According to studies, workers who believe they can have a positive impact on
their company would work harder, take more responsibility for their work, and
have happier lives overall. Through swift learning of fundamental Lean Six
Sigma skills, they can consistently simplify work, identify issues, and
decrease waste within a business.
Revolutionize your processes with Six Sigma precision
elevate quality, cut waste, and exceed expectations!
Benefits
to Implement 6 Sigma in Your Business
Benefits
to Implement 6 Sigma in Your Business
lean six sigma,
six sigma methodologies,
six sigma project management,
5s lean six sigma,
six sigma in operations management,
six sigma in quality management,
six sigma in manufacturing industry,
benefits of lean six sigma,
six sigma principles,
dmaic methodology in six sigma,
six sigma for quality control,
dmaic six sigma,
six sigma process,
lean management six sigma,
six sigma lean manufacturing,
six sigma in strategic management
The 5 Key Principles of Six Sigma
Serving the Customer
Maximizing consumer benefits should be the main goal of production changes. Market and customer expectations are set early on when a defined quality standard is established.
Recognizing and Focusing on Barriers
Six Sigma emphasizes identifying and addressing barriers to streamline processes. By recognizing and focusing on these obstacles, organizations can improve efficiency and deliver higher-quality products and services.
Getting Rid of Variations and Bottlenecks
Identify the problems, then create and put into practice solutions, similar to quality control programmes in many sectors of the economy. Simplifying these procedures improves output and quality assurance.
Training for Teams and Effective Communication
For Six Sigma success, ensure team understanding
and project transparency, as its meticulous execution can significantly
transform work environments.
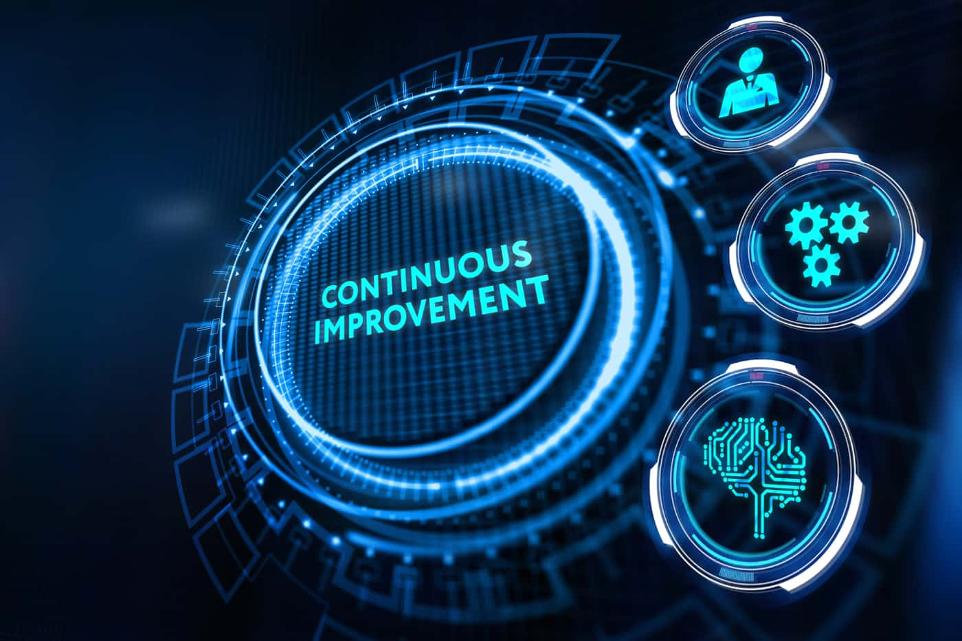
Adaptability and Responsiveness
Six Sigma drives innovation with precise problem-solving and continuous improvement, leading to significant business impact despite initial challenges.
Six
Sigma Fundamentals
The following are widely acknowledged as the fundamental components of the business theory and the characteristics that is:
Six Sigma Impact
The first step in the Six Sigma methodology is an end-to-end analysis. A customized solution design and implementation strategy are the result of this analysis. Every Six Sigma journey needs the teams' participation to be successful. We set up our clients' teams to eliminate functional silos and promote a culture of continuous development.
Average Productivity Increase
Average Lead Time Reduction
Average Inventory Coverage Reduction
Guidebook for Common Queries
1. What is Six Sigma?
Six Sigma is a data-driven methodology that improves process quality by identifying and removing defects and minimizing variability.
Six Sigma is a data-driven methodology that improves process quality by identifying and removing defects and minimizing variability.
2. How does Six Sigma improve business processes?
Six Sigma uses a structured approach called DMAIC (Define, Measure, Analyze, Improve, Control) to identify and eliminate inefficiencies, resulting in enhanced quality and cost savings.
Six Sigma uses a structured approach called DMAIC (Define, Measure, Analyze, Improve, Control) to identify and eliminate inefficiencies, resulting in enhanced quality and cost savings.
3. What are the key benefits of implementing Six Sigma?
Key benefits include reduced process variation, improved product quality, increased customer satisfaction, and significant cost savings.
Key benefits include reduced process variation, improved product quality, increased customer satisfaction, and significant cost savings.
4. How does Six Sigma differ from Lean manufacturing?
While
Lean manufacturing
focuses on reducing waste and improving flow, Six Sigma emphasizes reducing defects and variation. Both methodologies can be combined for optimal results.
While
Lean manufacturing
focuses on reducing waste and improving flow, Six Sigma emphasizes reducing defects and variation. Both methodologies can be combined for optimal results.
5. Can Six Sigma be applied to service industries?
Yes, Six Sigma is highly effective in service industries, helping to streamline processes, improve service quality, and enhance customer satisfaction.
Yes, Six Sigma is highly effective in service industries, helping to streamline processes, improve service quality, and enhance customer satisfaction.
6. How long does it take to see results from Six Sigma?
Results can vary based on the project's scope and complexity. Typically, noticeable improvements can be seen within a few months of implementation.
Results can vary based on the project's scope and complexity. Typically, noticeable improvements can be seen within a few months of implementation.
Let's Discuss Now
lean six sigma,
six sigma methodologies,
six sigma project management,
5s lean six sigma,
six sigma in operations management,
six sigma in quality management,
six sigma in manufacturing industry,
benefits of lean six sigma,
six sigma principles,
dmaic methodology in six sigma,
six sigma for quality control,
dmaic six sigma,
six sigma process,
lean management six sigma,
six sigma lean manufacturing,
six sigma in strategic management