lean manufacturing system,
lean in manufacturing industry,
lean management in manufacturing,
lean management,
lean management production,
lean manufacturing methodology,
benefit of lean management,
5s lean manufacturing,
downtime lean,
features of lean manufacturing,
lean manufacturing and management,
lean management system,
six sigma lean manufacturing,
benefits of lean,
lean manufacturing
What is LEAN?
The Lean methodology is centered on the principle of optimizing productivity and reducing waste in business operations. According to the lean concept, waste is defined as anything that doesn't create value that customers are ready to pay for.
Lean operations offer lower lead times, lower operational costs, and higher quality.
Boost Your Business with Lean Strategies & Achieve Remarkable Results!
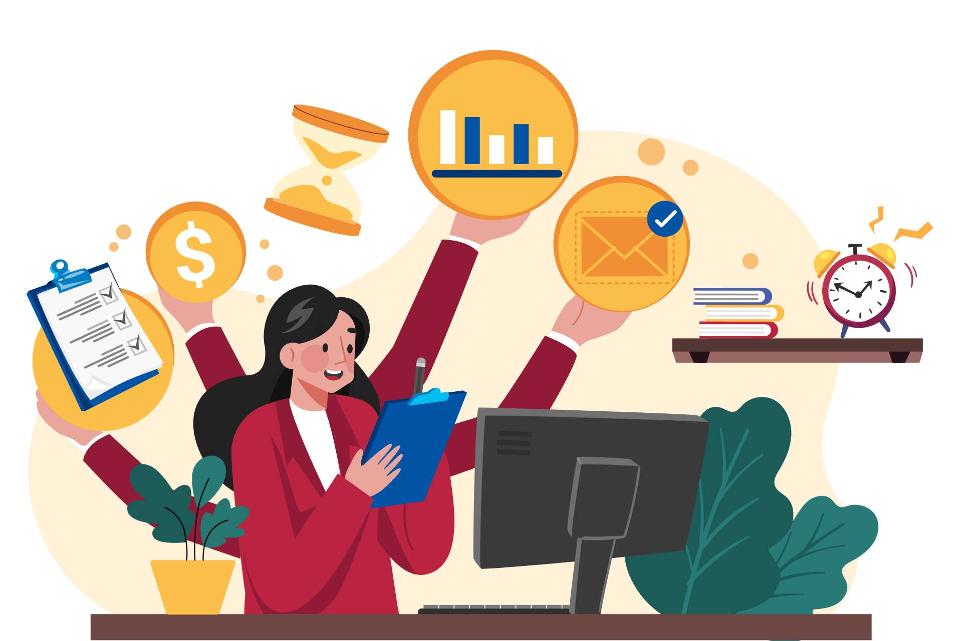
The goal of Lean for Business is to inspire customers to apply lean concepts to their businesses to boost productivity and competitiveness. Lean is not just for manufacturing organizations; it is for all businesses, regardless of industry.
By enhancing employees' ability to recognize difficulties, enhance processes, and create innovation, lean tools and practices are assisting companies worldwide in addressing challenges related to competition. Lean is, in short, about doing things better, faster, and less expensive. Lean aims to cut out waste and continuously develop a company.
So, don't wait and join the 1,000 Indian businesses that have successfully implemented Lean business strategies and seen notable profits, such as:
27% boost in productivity
42% increase in sales
38% improvements in delivery adherence
30% improvements in the quality of products and services
What are the 5 Principles?
The five main components that form the basis of lean manufacturing are value, value stream, pull, flow, and perfection. These principles form the foundation for implementing lean methodologies.
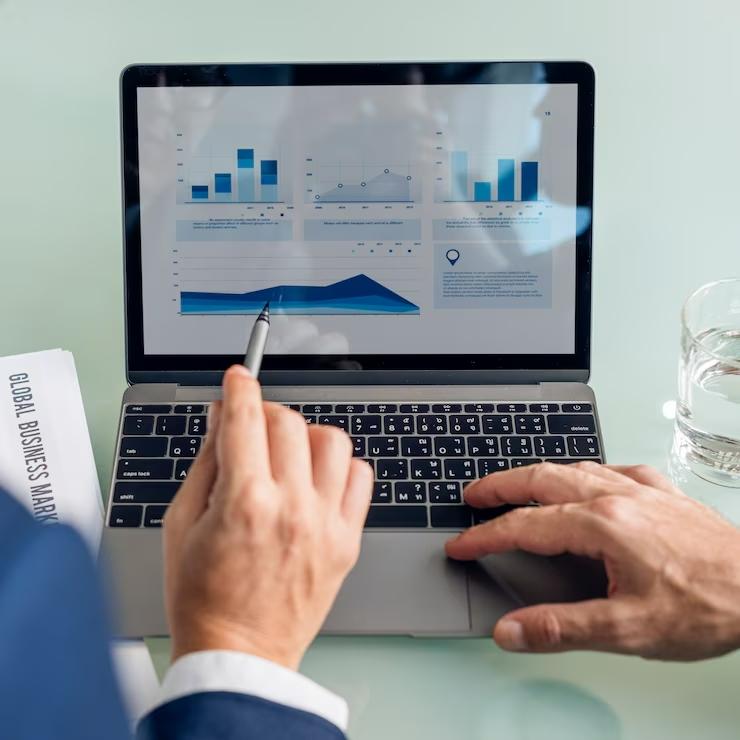
1. Value:
Value is evaluated from the customer's point of view and is related to the price they are prepared to pay for products or services. The manufacturer or service provider then creates this value by trying to reduce waste and expenses in order to meet the best pricing for the client and maximize profits.
2. Map the Value Stream:
In order to find waste and make changes, this principle requires evaluating the materials and other resources needed to produce an item or service. The value stream includes a product's whole lifecycle, from raw materials to waste. Waste must be found at every level of the manufacturing cycle, and anything that doesn't contribute value must be eliminated.
3. Create Flow:
Removing functional obstacles to shorten lead times is the process of creating flow. By doing this, procedures are guaranteed to run smoothly and to produce the least amount of waste or delay possible. In order to provide a steady stream of production or service delivery, flow must be established. Disrupted and discordant manufacturing processes are costly.
Streamline your success with Lean practices
it's time to trim the waste and amplify your efficiency!
4.
Establish a Pull System:
Pull systems operate by only starting up when there is a need. With output altered to match these sales or production projections, push systems calculate inventories ahead of time. However, this can lead to either too much or too little of a product being produced to fulfill demand because many projections are faulty.
Pull systems depend on adaptability, communication, and effective procedures to function well and only operate when there is demand. With the pull system, teams can only take on additional tasks after finishing the previous phases. This enables the team to adjust to difficulties as they come up because they know that the earlier work is still mostly relevant to delivering the product or service.
5. Perfection:
As defined by Kiichiro Toyoda, the founder of Toyota Motor Corporation, "Kaizen" refers to the ongoing process of improving processes to achieve perfection Continuous process evaluation and improvement are necessary for lean manufacturing to continuously eliminate waste and identify the ideal system for the value stream.
Metrics like lead times, cycles of production, efficiency, and cumulative flow must be measured in order for the concept of continuous improvement to have a significant and long-lasting impact on an organization.
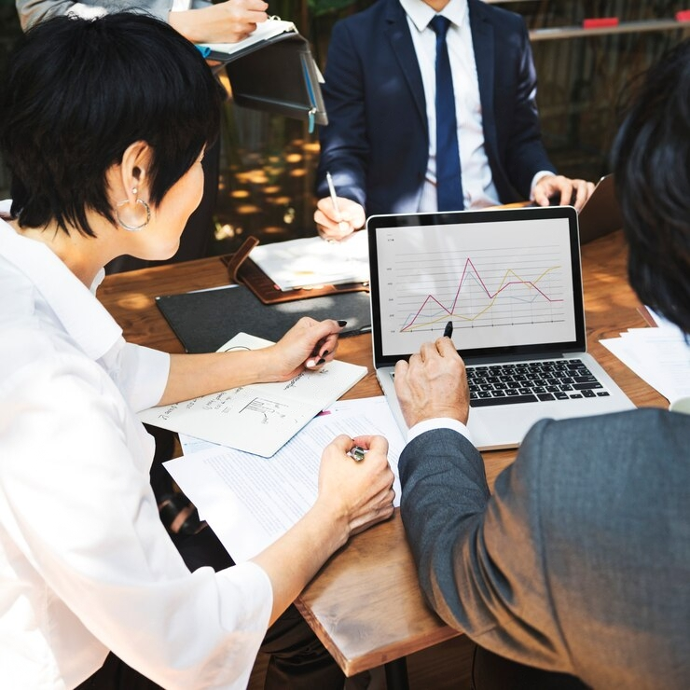
lean manufacturing system,
lean in manufacturing industry,
lean management in manufacturing,
lean management,
lean management production,
lean manufacturing methodology,
benefit of lean management,
5s lean manufacturing,
downtime lean,
features of lean manufacturing,
lean manufacturing and management,
lean management system,
six sigma lean manufacturing,
benefits of lean,
lean manufacturing
The 8 Wastes of Lean Manufacturing
D O W N - T I M E
Lean Implementation Benefits
Lean project management requires reducing or eliminating waste, but different people can benefit from lean manufacturing in different ways. While some claim it's boosting business profits, others insist the improvements are made only to add value for customers and raise their level of satisfaction. Here are some common goals.
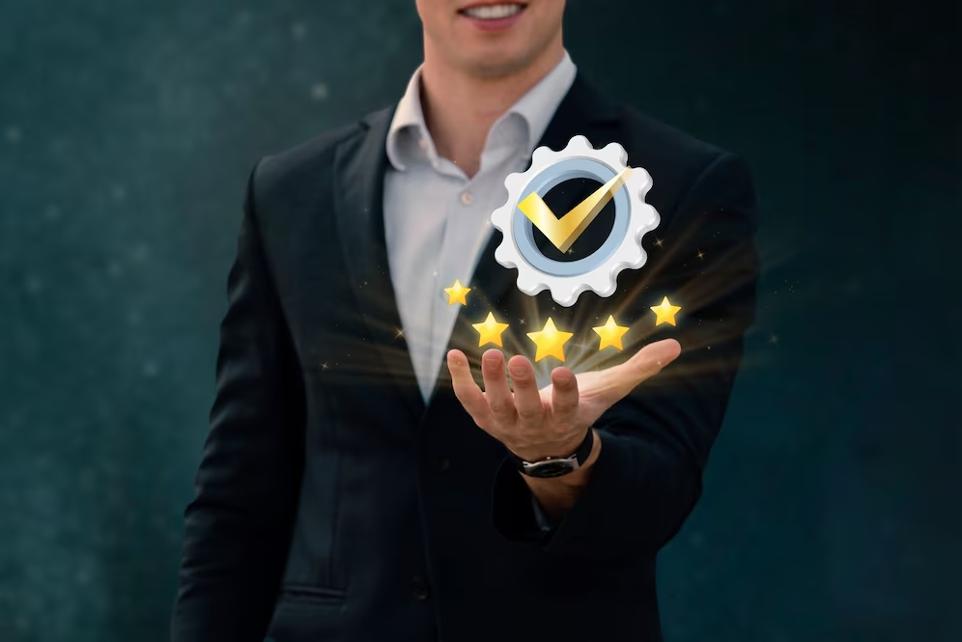
Improve Quality
To stay competitive, businesses must adapt to customer needs and desires, creating procedures that meet their expectations. Implementing overall quality management makes quality improvement a top priority.
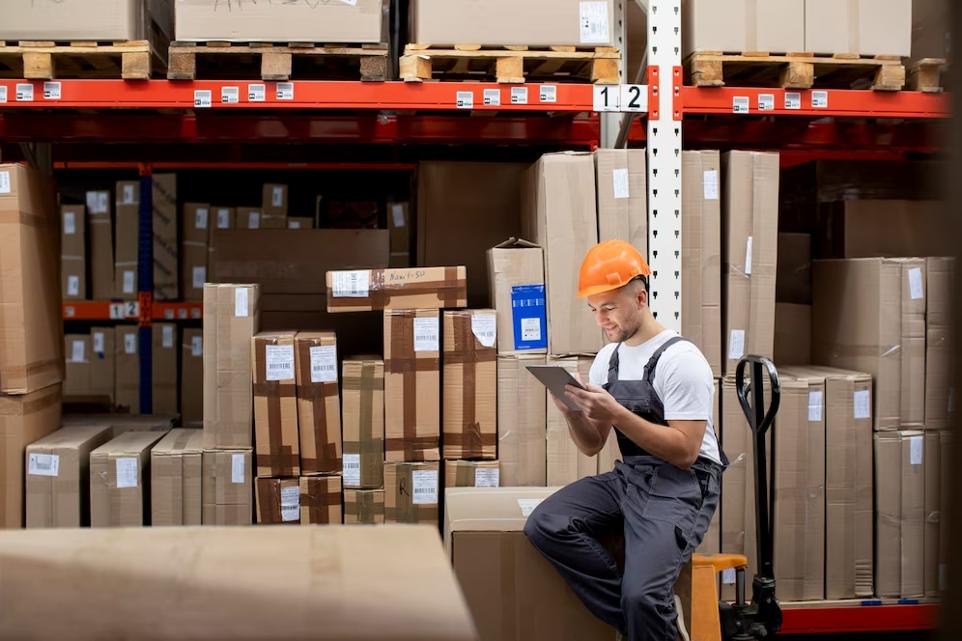
Inventory Management
Lean manufacturing decreases extra inventory, which lowers costs and avoids production problems, because of the just-in-time production technique.
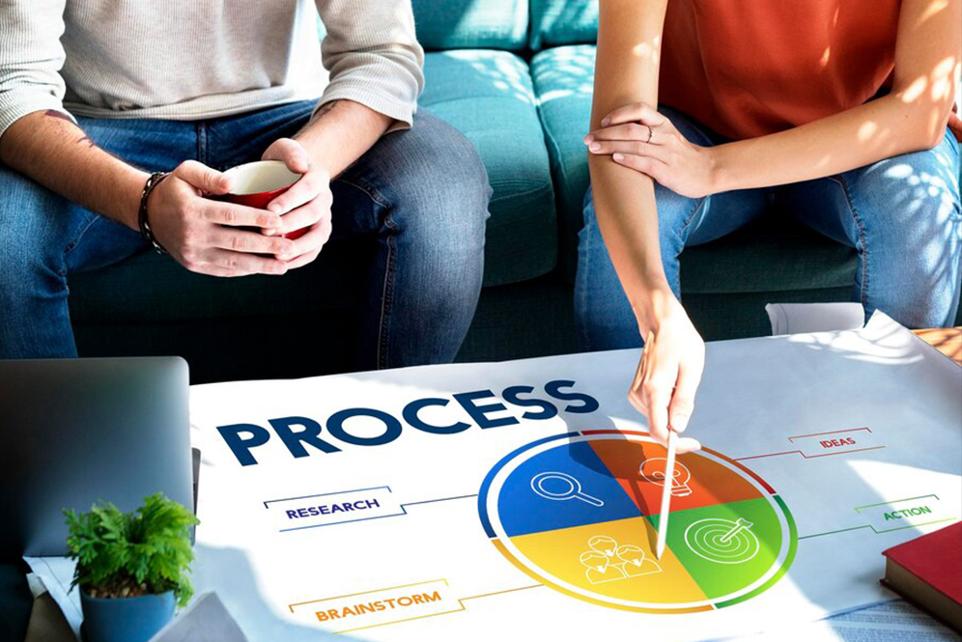
Process Improvement
The "continuous improvement" lean concept allows for the constant improvement of lean production processes. Value stream mapping is necessary in this situation.
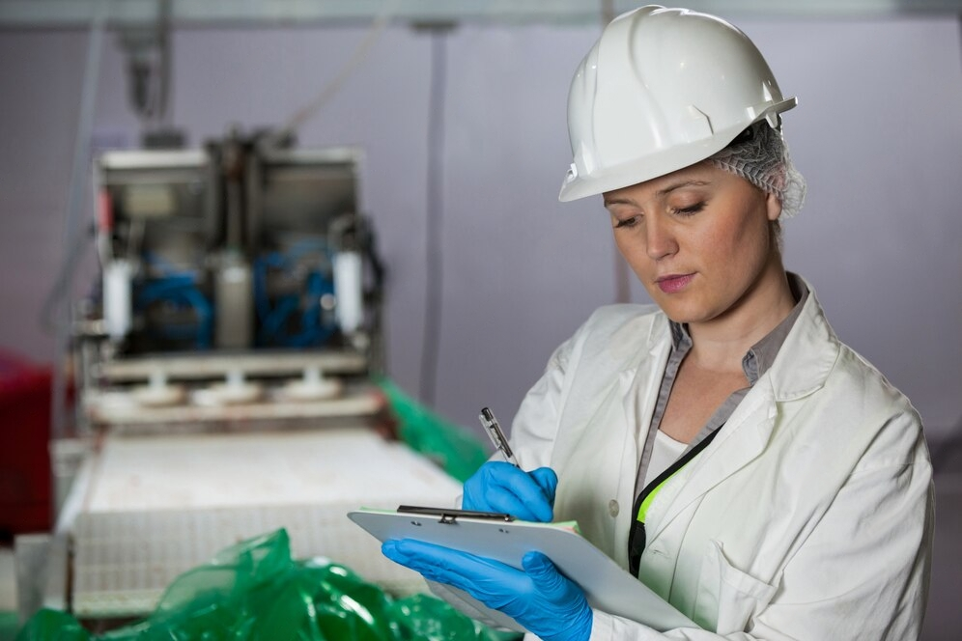
Eliminate Waste
Waste harms budgets, schedules, and available resources. It extracts without enhancing a product or service in any way. A lean manufacturing strategy can provide better products for less money by getting rid of waste.
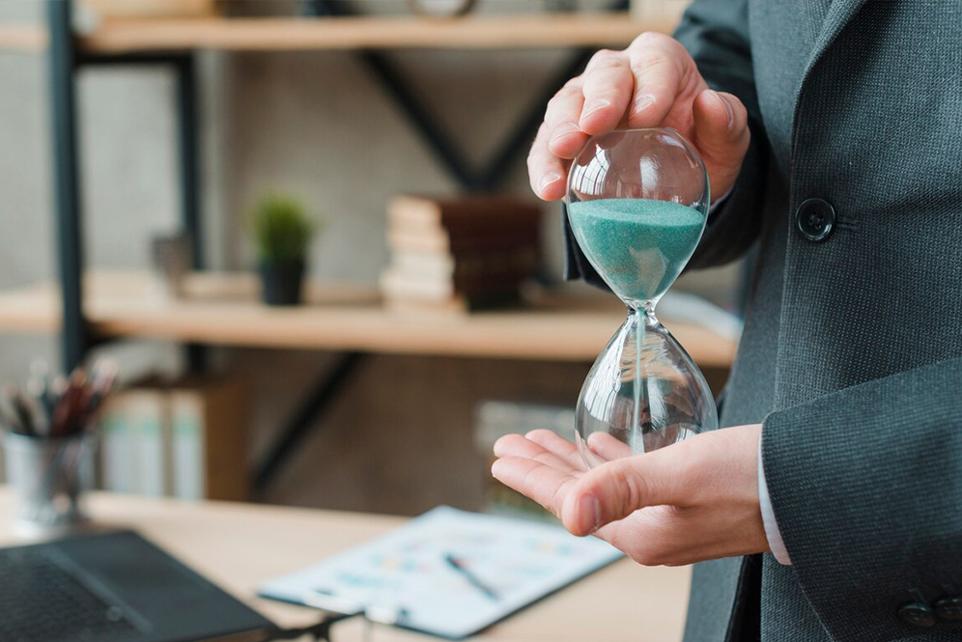
Reduce Time
Time is money, especially in manufacturing. Increasing efficiencies and implementing time management techniques reduce project start and completion times, adding value.

Reduce Total Costs
Efficient businesses save money by avoiding wasteful tasks and overproduction, which also reduces warehousing costs. Understanding the triple constraint is key to effective cost management.
Curious Minds Want to Know
1. What is Lean-based ERP software?
Lean-based ERP software
integrates lean manufacturing principles into enterprise resource planning systems to eliminate waste, simplify processes, and improve efficiency.
Lean-based ERP software
integrates lean manufacturing principles into enterprise resource planning systems to eliminate waste, simplify processes, and improve efficiency.
2. How does Lean-based ERP improve manufacturing efficiency?
Lean ERP improves manufacturing efficiency by optimizing
inventory management
, reducing production downtime, and enhancing real-time decision-making.
Lean ERP improves manufacturing efficiency by optimizing
inventory management
, reducing production downtime, and enhancing real-time decision-making.
3. Can Lean-based ERP software be customized for my business?
Yes, Lean-based ERP software can be customized to meet the specific needs of your business, including custom workflows, reporting, and integration with existing systems.
Yes, Lean-based ERP software can be customized to meet the specific needs of your business, including custom workflows, reporting, and integration with existing systems.
4. How does Lean ERP differ from traditional ERP systems?
Lean ERP focuses on eliminating waste and enhancing process efficiency, whereas traditional ERP systems may not be highly focused on these lean principles.
Lean ERP focuses on eliminating waste and enhancing process efficiency, whereas traditional ERP systems may not be highly focused on these lean principles.
5. What is the ROI of implementing Lean-based ERP software?
The ROI of Lean-based
ERP software
includes reduced operational costs, increased productivity, and faster time-to-market, leading to a more profitable and efficient business.
The ROI of Lean-based
ERP software
includes reduced operational costs, increased productivity, and faster time-to-market, leading to a more profitable and efficient business.
6. How long does it take to implement Lean ERP?
The implementation timeline varies based on the complexity of your business needs and the size of your organization, but it typically ranges from a few months to a year.
The implementation timeline varies based on the complexity of your business needs and the size of your organization, but it typically ranges from a few months to a year.
7. What are the key features of Lean ERP software?
Key features include inventory management, demand forecasting, production scheduling, quality control, and real-time data analytics.
Key features include inventory management, demand forecasting, production scheduling, quality control, and real-time data analytics.
Let's Discuss Now
lean manufacturing system,
lean in manufacturing industry,
lean management in manufacturing,
lean management,
lean management production,
lean manufacturing methodology,
benefit of lean management,
5s lean manufacturing,
downtime lean,
features of lean manufacturing,
lean manufacturing and management,
lean management system,
six sigma lean manufacturing,
benefits of lean,
lean manufacturing