How You Can Reduce Wastages From Business Operations and Automate Business Through Lean-based ERP
In the modern business landscape, Productivity is important. Every business, whatever size or industry, continually seeks ways to optimize its operations, reduce wastage, and increase profitability. One of the most effective tools for achieving these goals is implementing Enterprise Resource Planning software (ERP). But Let’s see how exactly ERP can help to automate business processes and to minimize wastages. Let’s dive in.
Understanding Lean ERP
What is Lean ERP?
Lean ERP is a software solution that integrates lean manufacturing principles into ERP systems. The goal of lean manufacturing is to remove non-value-added processes to reduce waste and increase efficiency. When combined with ERP, it creates a system that manages business processes more effectively.
Core Principles of Lean ERP
Lean-based ERP is built on several core principles:
- Value Stream Mapping: Recognising and evaluating the information and material flow.
- Continuous Improvement: Always looking for methods to make procedures better.
- Elimination of Waste: Reducing or eliminating non-value-added activities.
- Just-In-Time Production: Producing only what is needed when it is needed.
Streamlining Processes with Automation
One of the key advantages of Lean ERP is its ability to automate repetitive and time-consuming tasks. Processes speed up by automation, which also removes human mistakes and increases reliability and productivity. Here are some areas where Lean-based ERP can automate processes:
(1) Inventory Management:
Lean ERP systems utilize advanced algorithms to optimize inventory levels, ensuring that businesses have a sufficient quantity of stock on hand when they need it. By automating
inventory management, businesses can avoid overstocking or stockouts, both of which contribute to wastage. Lean-based ERP also enables real-time tracking of inventory, reducing the risk of outdated or destroyed products.
(2) Production Planning and Scheduling:
Lean ERP systems automate production planning and scheduling by evaluating several variables such as demand forecasts, production capacity, and resource availability. This confirms that production processes are optimized, reducing inactive time and minimizing the risk of overproduction. By lining up production schedules with actual demand, businesses can significantly decrease wastage.
(3) Procurement and Supplier Management:
Automating procurement processes with Lean ERP simplifies the entire supply chain. From generating purchase orders to tracking deliveries, Lean ERP ensures that procurement activities are efficient and authentic. Additionally, Lean-based ERP systems facilitate better supplier management by providing real-time insights into supplier performance, lead times, and quality. This enables businesses to make informed decisions, reducing the risk of procurement-related wastage.
(4) Quality Control:
Lean ERP systems integrate quality control processes into the production workflow, confirming that products meet the required standards at every stage. By automating quality control, businesses can detect defects early, reducing the likelihood of rework or product places. This reduces waste and improves customer satisfaction levels.
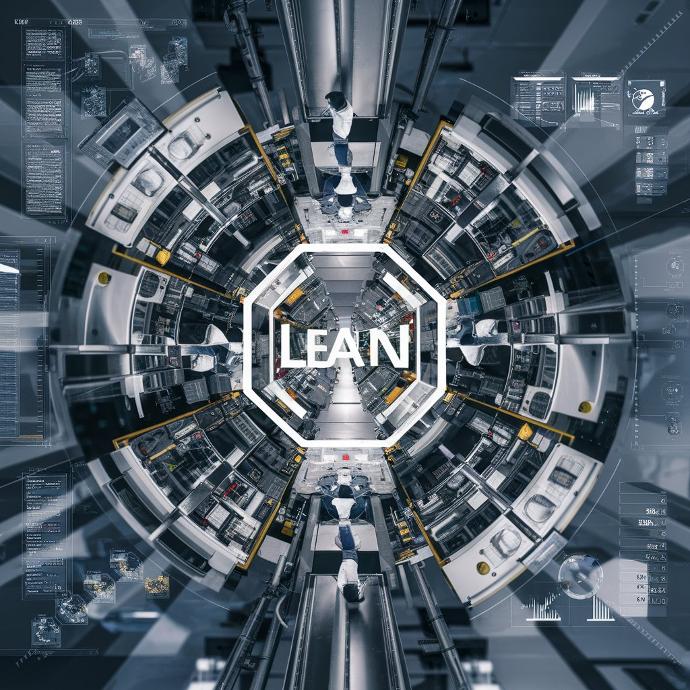
Don't Just Read About Success,
Take the Next Step
Let's Schedule a Consultation Meeting
Minimizing Wastage Through Lean Principles
Lean-based ERP includes various lean principles that are specifically designed to minimize waste in business operations. Here are some key principles and how they are applied in
Lean-based ERP systems:
(1) Just-In-Time (JIT) Inventory:
Lean-based ERP systems allow businesses to adopt a Just-In-Time inventory approach, where materials and parts are delivered exactly when needed. This eliminates the need for excessive inventory storage, reducing carrying costs and the risk of outdatedness. By coordinating supply with demand, businesses can minimize waste and improve cash flow.
(2) Continuous Improvement (Kaizen):
Lean ERP promotes a culture of continuous improvement, encouraging employees at all levels to identify and eliminate waste. The system provides real-time data and analytics, empowering teams to make data-driven decisions and implement process improvements. By continuously optimizing operations, businesses can achieve long-term waste reduction and operational excellence.
(3) Value Stream Mapping:
Value stream mapping is a lean tool used to visualize and analyze the flow of materials and information throughout the production process. Lean ERP systems integrate value stream mapping, allowing businesses to identify bottlenecks, inefficiencies, and areas of waste. By optimizing the value stream, businesses can streamline processes and reduce lead times, ultimately minimizing wastage.
(4) Standardized Work:
Standardized work involves defining and documenting the most efficient way to perform tasks. Lean ERP systems facilitate the creation and maintenance of standardized work procedures, ensuring consistency and reducing variability. By standardizing processes, businesses can eliminate unnecessary steps, reduce errors, and improve overall efficiency.
Real-World Benefits of ERP Implementation
Srivaru Motors Pvt. Ltd. Company, that have implemented
ERP systems
has seen particular benefits in terms of waste reduction and operational efficiency. For instance, a manufacturing company reported a 20% reduction in raw material wastage after implementing an ERP system. Similarly, a retail business saw a 15% decrease in stockouts and overstock situations, leading to significant cost savings.
Final Thoughts
Implementing Lean ERP systems can revolutionize business operations by automating processes and minimizing waste. By streamlining inventory management, production planning, procurement, and quality control, Lean ERP ensures that resources are used efficiently and waste is minimized. Additionally, lean principles such as Just-In-Time inventory, continuous improvement, value stream mapping, and standardized work further contribute to waste reduction.
Ready to revolutionize your business operations and reduce waste? Embrace ERP solutions today and unlock the full potential of automation and efficiency. Contact us at Technovative Solution to learn how our ERP consulting services can help you streamline your processes and achieve operational excellence.
Read Also: What is Lean-based ERP Software: A Complete Guide for Your Manufacturing Business
Unraveling the Mysteries
(1) What is Lean ERP, and how does it help in reducing wastage in business operations?
Answer: Lean ERP integrates lean manufacturing principles with enterprise resource planning systems. It helps reduce wastage by streamlining processes, improving resource allocation, and minimizing non-value-added activities.
(2) How does Lean ERP contribute to waste reduction in the supply chain?
Answer: Lean ERP enhances supply chain visibility and coordination, allowing businesses to identify and address inefficiencies. Streamlining procurement, logistics, and communication with suppliers, reduces delays, overproduction, and other forms of waste in the supply chain.
Don't Wait for the Right Time,
Let's Talk & Implement it
Let's Schedule a Consultation Meeting
Reduce Wastages, Business Operations, Automate Business, Lean-based ERP, Lean Manufacturing, Inventory Management, Manufacturing ERP Software, ERP System, ERP Software, Production ERP Software